Pneumatic conveying systems are common methods to transfer powders, granules, and other dry bulk materials. However, understanding this conveying technology is often a challenging task. In this article, we will address what a pneumatic conveying system or a pneumatic handling system is? We will check out the types of conveying systems and the advantages of pneumatic conveyors. Lastly, we’ll see why people should utilise pneumatic conveying systems for dry bulk material handling and processing plants.
A] What is Pneumatic Conveying System?
Pneumatic conveying system transfers powdered material, granules and other dry bulk material through an enclosed pipeline in a factory setup. The motive force to transfer these granules or particles comes from a combination of pressure differential and the flow of gas, including air or nitrogen.
The system’s basic elements include:
- A fan or a blower
- A feeder or a similar material introduction device
- A conveying line or a con veyor belt
- A terminal vessel along with the dust collection system.
Some of the most common materials transferred by a pneumatic conveying system include flour, cement, sand, plastic pallets, and hundreds of chemicals, food products and minerals. Materials that are semi-dry or in the form of paste or slurry are typically not suited for pneumatic conveying.
A standardised conveying mechanism operates in a straight line and requires adjustment in the direction. It is operated with a motor driven for the directional shift.
On the contrary, the pneumatic conveying mechanism uses a basic pipeline to transfer the material. The entire system is enclosed and has very few moving parts that are electronically managed. The system is completely dust-free, making it easier to maintain.
Ready to Upgrade Your Material Handling? Get Started Today
B] Framework of Pneumatic Handling System
Three basic frameworks are used to generate a high-velocity air stream in the pneumatic handling (conveyor) system.
1. Suction or vacuum conveying system: This system is used to draw material with the ambient air using a vacuum produced in the pipeline. The system is operated at a lower pressure, which ranges between 0.4 to 0.5 bar (g). The pressure is primarily used to move light-weight products.
2. Pressure type system: The system uses a positive pressure to move the material from one destination to another. This device is used for moving material from one loading point to another unloading location.
3. Combination system: This system employs a suction device to transfer the material from the loading point and uses pressure methods to move it to a range of unloading points.
C] Types of Conveying Systems
The pneumatic handling system can be classified based on its operating principles. The system follows two operating principles: dilute phase and dense phase. Each phase can either run under pressure or vacuum. Each pneumatic conveying system is used for different applications and includes different functions.
1. Dilute Phase Pneumatic Conveying
The dilute phase conveying system uses gas velocity of greater than 17-18 m/s with lower vacuum or pressure. The dilute phase, also referred to as the lean phase pneumatic conveying system, depends on the momentum of the air stream to transfer the particles along with keeping them in suspension in the conveyer.
In dilute phase conveying, the material is suspended within the air, and the solid loading ratio is significantly lower. The system is ideal for conveying non-abrasive materials that have low bulk density.
Some common applications of the dilute phase system involve:
- Transferring non-abrasive material like flour
- Products that cannot break easily
- Light bulk density materials
In the dilute phase system, the material never settles at the bottom of the pipeline. The intake velocity of the system is often regarded as the most important area, and at this stage, the air is at the lowest intensity. The lean phase system is most commonly used for granules and powders.
A dilute phase conveying system has well-optimised velocity and therefore, requires minimal energy consumption. A major advantage of the dilute phase system is its flexibility. This system is often used to convey a wide range of materials that cannot be conveyed in a dense phase system like maize and other flours.
2. Dilute Phase Pneumatic Conveying
To transfer sensitive or fragile products, dense phase conveying systems are often ideal. This type of conveying system transfers material whose particles are either heavy, enormous, or fragile. As heavier particles cannot remain suspended in the airflow it is hard to convey large molecules due to the high-velocity air in the system. These systems are used to handle and transfer products at lower velocities as it helps to prevent impact damage to the product.
A dense phase system employs pulses of air to push the product followed by another pulse of both air and product. The dense phase system requires more precise calculations due to its design.
Common applications for dense phase systems involve:
- Materials with heavy densities
- Abrasives
- Blended products
- Friable materials like carbon black prills
- Plastic pellets and other items that do not require continuous delivery
Based on the application specifications and the product that needs to be handled and transferred, the right pneumatic conveying system can be employed. A pneumatic conveying system is custom-designed to fit the existing processing equipment, thereby offering more flexibility.
D] Why Choose Pneumatic Conveying Over Mechanical Conveying?
To understand the advantages of the pneumatic conveyor system, let’s start by looking at and understanding a mechanical conveying system.
- A conventional mechanical conveying system runs in a straight line and has many directional changes. Each conventional mechanical conveying system requires its own motor and drive. The mechanical conveying system may be open rather than closed, as it potentially generates dust. The system also has a relatively large number of moving parts that require frequent maintenance. The system tends to take up a lot of valuable real estate in a factory or a plant.
- On the contrary, a pneumatic conveyor system employs a simple and small diameter pipeline to transfer the powdered material. The conveyor offers great cost-effectiveness when conveying in higher capacities as well as over long distances. The conveyor pipeline can be arranged around existing equipment making the system more flexible, with relatively small footprints. The system is fully enclosed and has few moving parts.
E] Advantages of Pneumatic Conveyors
Let’s check the advantages of a pneumatic conveyor system. A pneumatic handling system usually offers:
- Dust-free operation at the production facility
- All materials remain sanitary and promote a hygienic facility
- The system employs simpler methods for product pickup and process
- The system requires very low maintenance
- It prevents any product leakage or contamination
- The system helps in increasing the safety of the operators as well as the maintenance workers
- The system requires very little space, as the material is conveyed through pipes
- The system is quick to install and easy to maintain
Ready to Upgrade Your Material Handling? Get Started Today
To Sum Up
Once you have decided on a dilute or dense phase pneumatic conveying system, it is important to determine whether the system should operate under pressure or vacuum. It is advisable to conduct a test with the same material that the conveying system will handle in the plant. This involves considering the system with the same conveying mechanism as well as route, along with the conveying line length and number of installed bends in the system.
The basic criteria for testing the system should include:
- Whether the proposed system conveys the material
- At what rate the material is conveyed
- How much air the system consumes to convey the material ?
- It is also important to define the criteria for the application, such as conveying a friable material.
- The supplier should also test the system to understand the size the conveying system will handle.
Elements to consider when looking at the system:
- Temperature
- Air humidity
- Particle size and shape
- Moisture content
- Concentration
- System distance
- Density
- Angle of flow
Need help choosing the right pneumatic handling system for your application? We can help! Get in touch with us today.
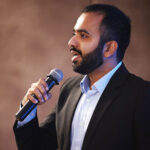
Kedar Kamath
Kedar Kamath is a highly accomplished bulk material handling professional with 14+ years of experience at Macawber Engineering Systems India Pvt Ltd. Starting as a junior sales engineer, he progressed to his current role heading Business Development and Sales. His expertise encompasses proposals, estimations, sales, marketing, design engineering, project execution, and factory operations. Mentored by industry leaders, Kedar's technical acumen (B.Tech in Electrical Engineering, VJTI, Mumbai) and innovative approach deliver tailored solutions. He's passionate about sustainable practices and driving excellence within the industry.