Pneumatic Conveyor For Plastic
- Home
- Industries
- Plastic
Enquire Now
Please Feel Free to Fill out the Form below with your requirements. We will get back to you within 1-2 business days.

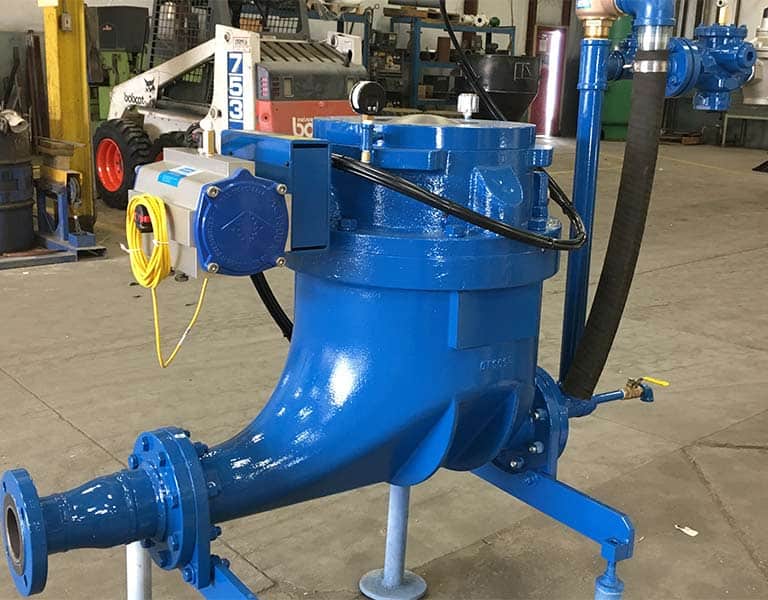
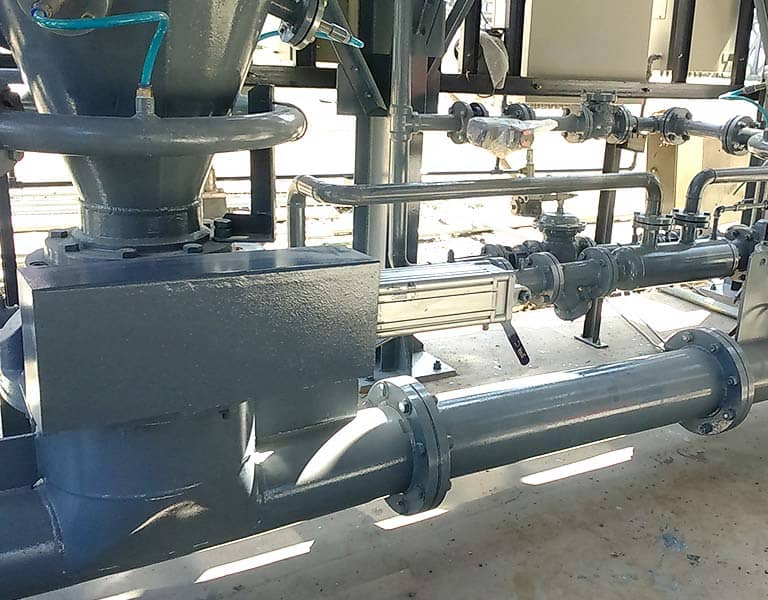
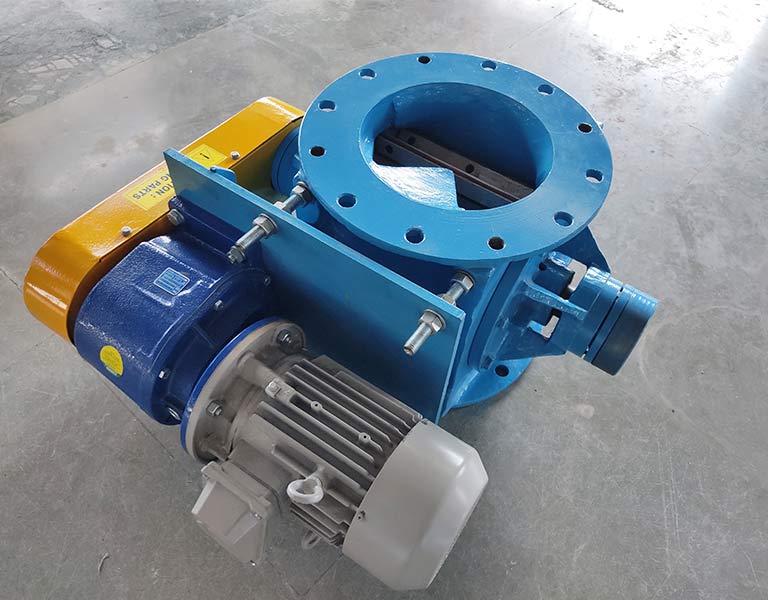
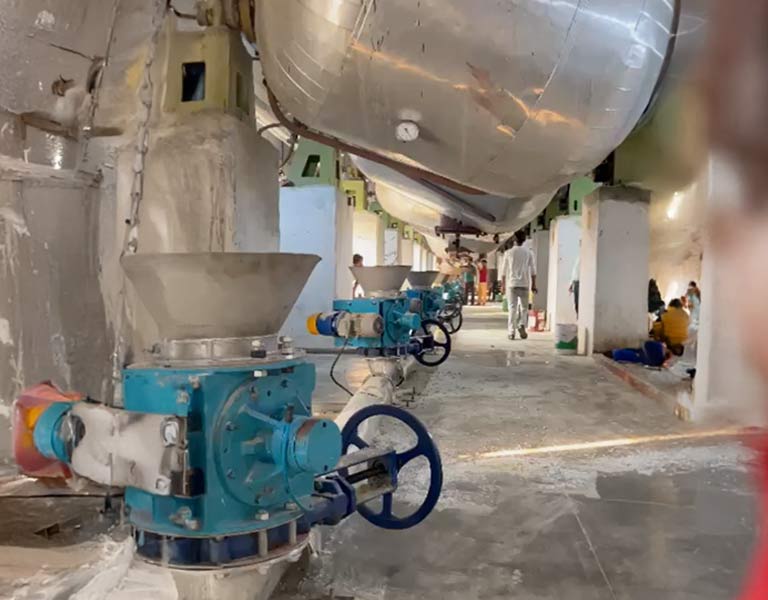
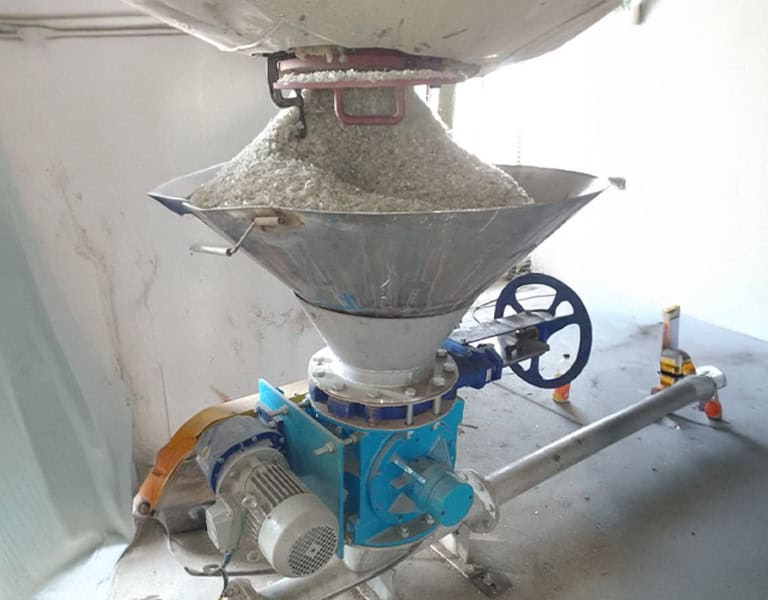
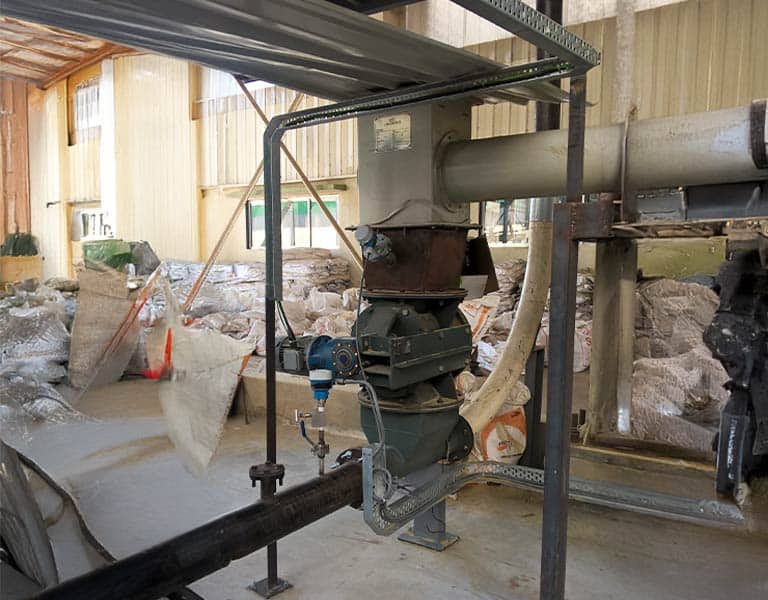
Pneumatic Conveying in the Plastic Industry
The plastic industry is a global sector focused on the production and manufacturing of plastic materials and products. It plays a vital role in various industries, including automotive, packaging, construction, and healthcare. Innovations in plastic production have led to advanced, durable, and cost-effective solutions, driving economic growth worldwide.
Pneumatic conveying in the plastic industry efficiently transports bulk materials, such as plastic pellets, powders, chips, and granules, through pipelines using air pressure. Pneumatic conveying of plastic enhances automation, reduces manual handling, and ensures a smooth, contamination-free transfer process. This technology improves productivity, safety, and material flow in plastic manufacturing and processing.
Achieve smooth and efficient plastic material handling with our advanced pneumatic conveying solutions.
Solutions offered by Macawber
- Dense phase pneumatic conveying system: Macawber has supplied various dense phase pneumatic conveying systems to clients from the plastic and polyester industries, successfully handling resin powder, PVC dry blend powder, polyester chips, and hot PET chips. The Denseveyor is a key piece of equipment in these systems. We offer dense phase solutions with capacities ranging from 1 TPH to 50 TPH over distances of up to 300 meters, or subject to application.
- Lean phase positive pressure pneumatic conveying system: We have provided positive pressure lean phase pneumatic conveying systems for conveying PET bottle caps and PET flakes in the plastic industry. In a bottle cap manufacturing facility, our dump valve—key to diverting caps into cooling and curing silos—has successfully handled 1 million caps per day. Additionally, in a recent project, we conveyed PET flakes from jumbo bags to 10 air dryers and subsequently from their outlets to three silos.
- Lean phase negative pressure pneumatic conveying system: Macawber also supplies lean phase negative pressure pneumatic conveying systems for the plastic industry, including a system designed for polyester chip handling. The system, which meets the customer’s capacity requirement of 2 TPH, was supplied to one of the major players in the polyester manufacturing industry.
- Ash handling system: In plastic industry plants with captive energy generation, handling ash in compliance with environmental regulations is a significant challenge. Macawber addressed this challenge by supplying an ash-handling system, with the Ashveyor, equipped with Macawber’s Dome valve, as the key equipment.
- De-dusting system: Macawber India offers a range of dust extraction solutions, including bin vent filters and bag filters with suction ducts. For a leading manufacturer of plastic chips and filament yarns, we supplied a de-dusting system that not only achieved a clean working environment but also facilitated the recovery of useful dust.
- Automation: Macawber’s automated pneumatic conveying for the plastic industry enhances operational efficiency, accuracy, and safety. By integrating sensors, controls, and real-time monitoring, we optimise material flow, reduce human intervention, and ensure precise delivery, all while minimising downtime and improving overall reliability.
Macawber Products Supplied
- Denseveyor
- Ashveyor
- Dome valves
- Diverter valves
- Bag filters
- DV-type Diverter valve
- Wear-resistant bends
- Bin vent filters
- Cyclonic separator
- Rotary Airlock Valve
Unique Selling Points (USPs) of Our Design
- ASME Compliance: Macawber emphasises ASME standards when designing pressure vessels for pneumatic dense-phase conveying, ensuring safety, efficiency, and compliance. Adhering to specific codes and guidelines guarantees reliable operation.
- Dome Valves: The dome valve, crucial for regulating bulk powder flow, is the most wear-prone component. Macawber's dome valves feature special hard coatings tailored to material properties and customer requirements, including ceramic, tungsten carbide, and frit coatings.
- Rotary airlock valves: Designs customized to handle plastic flakes with special non-pinching designs and venting arrangements suited for handling flakes.
- Heavy-Duty Design for Long Life: Macawber's pneumatic conveying systems have been successfully supplied over the past 30 years across the Indian plastic industry, thanks to a focus on heavy-duty design that results in an extended equipment lifespan.
- Optimal Sizing Design: Based on the required conveying capacity and corresponding air requirements, Macawber optimises vessel and pipeline sizes to meet critical performance parameters and energy efficiency.
- Healthy Filtration Area: Proper venting of air is essential before material is dropped at reception points. An inadequate filtration area can lead to back pressure and system malfunctions. Macawber prioritises a healthy filtration area for efficient venting.
Macawber is the leading pneumatic conveying system manufacturer in India for a number of industries. We specialise in crafting precise solutions for all conveying needs. Get in touch with us to learn more about pneumatic conveying systems for the plastic industry.
Achieve smooth and efficient plastic material handling with our advanced pneumatic conveying solutions.
Frequently Asked Questions
A pneumatic conveying system transports plastic materials like pellets, powders, and flakes through pipelines using air pressure or vacuum. This method ensures efficient, contamination-free, and automated material transfer in plastic manufacturing.
A pneumatic conveyor for the plastic industry can be used for transporting a wide range of plastic materials, including resin powders, PVC dry blends, polyester chips, PET flakes, and plastic pellets. Both dense-phase and lean-phase systems are used based on material characteristics and application needs.
Pneumatic conveying enhances automation, reduces manual handling, and prevents contamination during material transfer. It also improves productivity, safety, and overall material flow in plastic manufacturing processes.
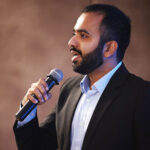
Kedar Kamath
Kedar Kamath is a highly accomplished bulk material handling professional with 14+ years of experience at Macawber Engineering Systems India Pvt Ltd. Starting as a junior sales engineer, he progressed to his current role heading Business Development and Sales. His expertise encompasses proposals, estimations, sales, marketing, design engineering, project execution, and factory operations. Mentored by industry leaders, Kedar's technical acumen (B.Tech in Electrical Engineering, VJTI, Mumbai) and innovative approach deliver tailored solutions. He's passionate about sustainable practices and driving excellence within the industry.