In the recycling of PET (Polyethylene Terephthalate) flakes, efficiency, cleanliness, and automation are critical for consistent production and quality. One such successful application was the design and installation of a PET flakes conveying system, engineered to transport PET flakes from Jumbo Bags to inline dryers in a PET recycling facility. The plant converts waste PET bottles into plastic fibres (source), which are then used across various industries.
How to Transport PET Flakes in a Recycling Plant: A Lean Phase Solution
Key Challenges in PET Flakes Handling
- Low Bulk Density: PET flakes have a low bulk density of around 350 kg/m³, requiring high air-to-material ratios for effective transport. This not only increases energy consumption but can also reduce system efficiency and load consistency, particularly over long distances or with vertical lifts in pneumatic conveying for PET flakes. In order to overcome this issue it is imperative to employ a lean phase conveying design for low bulk density materials. This ensures flow control without compromising material integrity.
- Flaky & Irregular Shape: Due to their flaky and lightweight structure, PET flakes often exhibit poor flow behaviour. They can float within the conveying line or become airborne, resulting in inconsistent conveying, flow interruptions, and difficulties in maintaining a uniform feed rate without proper system tuning or material conditioning.
- Bridging in hoppers: PET flakes have a tendency to interlock and bridge inside hoppers, leading to material flow blockages. This disrupts conveying and can cause equipment downtime. Specialized hopper geometry and flow aids like vibration, fluidisation pads, or agitators are often required to promote consistent discharge.
- Degradation and Fines Generation: High-speed or poorly configured conveying systems can cause PET flakes to break down into fines. These fines may compromise product quality, clog filters, and increase dust emissions, leading to frequent cleaning, maintenance, and potential downstream processing issues in dryers or extruders.
- Dust Control: Although PET flakes are not highly dusty by nature, fines generated during handling can create significant dust clouds. This impacts air quality and demands high-efficiency filtration and can pose fire or explosion hazards if not addressed with proper dust extraction and containment solutions.
- Material Routing Complexity: Handling PET flakes in systems with multiple destinations, such as dryers or extruders, introduces routing challenges. Diverter valves must switch accurately without jamming, and control systems need to coordinate destinations precisely. Any malfunction can result in misrouting, material loss, or process interruption in an automated material routing system.
Streamline PET flake transfer with the help of our lean phase conveying solutions.
Project Overview
The system begins with PET flakes being loaded into a Feed Hopper using an electric hoist. A rotary airlock valve for PET flakes fitted at the hopper’s outlet ensures a uniform flow of flakes into the conveying line. The material is then conveyed using a Roots Blower, which generates positive pressure to transport the flakes through the pipeline.
A network of long-radius bends and a strategically placed Macawber T-type dump valve diverter ensures accurate delivery to one of ten inline dryers. The diverter, pneumatically actuated, has a 1-inlet and 2-outlet design and can shift flow either inline or perpendicular, depending on the destination dryer selected via PLC-based logic.
This system’s flexibility allows it to serve all ten dryers through a single pipeline, one at a time, and then move on to stage two, where the material is routed to one of three extruder hoppers. This supports efficient material handling in PET recycling
Key System Advantage
- Lean System Design: A single feed point connects to multiple dryers; Stage 2 allows multiple feed hoppers to serve a few destinations, ensuring efficient and streamlined material routing.
- Simple Layout: T-type dump valve diverters enable direct routing to destinations. This minimises pipeline complexity and simplifies system design and maintenance.
- Robust Construction: Engineered for PET flakes, the system resists jamming and clogging, ensuring consistent performance under demanding recycling conditions with varying flake sizes and flow characteristics.
- Rotary Valve Innovation: Special non-pinching rotary valve design prevents PET flakes from getting trapped, ensuring uninterrupted material flow and protecting against equipment damage or flow obstruction.
- Automated Operation: Integrated with PLC-SCADA, the system allows automated routing, real-time monitoring, and smooth operation with minimal manual intervention, boosting plant productivity and control.
- Cleaner Operation: Fully enclosed design minimises dust emissions and material spillage, enhancing workplace cleanliness, operator safety, and compliance with food-grade and environmental standards.
- Tailored Engineering: System layout and components are customised to meet site-specific requirements, optimising performance, space utilisation, and ease of integration within the customer’s plant operations.
Products Handling PET flakes
Macawber offers a range of products that effectively handle PET flakes, including:
- Pickup tee
- Diverter valves
- Bag filters
Streamline PET flake transfer with the help of our lean phase conveying solutions.
This lean-phase pneumatic conveying for PET flakes system is a benchmark in material handling automation. It reflects a fine balance of custom engineering, process control, and system reliability, ensuring consistent feed to dryers and extruders while minimising losses. Designed with future scalability in mind, this solution lays a strong foundation for high-output, hygienic, and sustainable PET recycling operations.
In conclusion, Macawber Engineering’s innovative solutions and commitment to quality position it as a leader in ash conveying, addressing the unique challenges associated with this material.
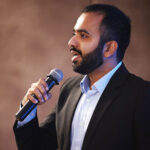
Kedar Kamath
Kedar Kamath is a highly accomplished bulk material handling professional with 14+ years of experience at Macawber Engineering Systems India Pvt Ltd. Starting as a junior sales engineer, he progressed to his current role heading Business Development and Sales. His expertise encompasses proposals, estimations, sales, marketing, design engineering, project execution, and factory operations. Mentored by industry leaders, Kedar's technical acumen (B.Tech in Electrical Engineering, VJTI, Mumbai) and innovative approach deliver tailored solutions. He's passionate about sustainable practices and driving excellence within the industry.