Since handling fly ash in conveying system can lead to wear, dust, plugging and erosion, understanding its various challenges can help prevent downtime and reduce damage to the system.
Fly ash is a residual product of coal (or solid fuel) combustion, compromising of fine particles that are released from the cold-fired boilers via flue (exhaust) gases. As a by-product, fly ash is reused to create building materials similar to Portland cement and hollow blocks. However, owing to its fine size, handling fly ash can be difficult.
In this article, we’ve covered the various challenges of handling fly ash, its uses, and how a robust fly ash handling system can help tackle these issues.
Learn How Fly Ash Is Transforming the Cement Industry
A] Fly Ash Handling Challenges
The method of collecting, conveying, interim storing and loading residual ash from solid fuel combustion processes is called Ash Handling.
Fly ash handling includes a pressure or vacuum transportation system that helps collect ash using electrostatic precipitators (ESPs) or other apparatus in the flue gas processing stream. The collected fly ash is then transported hydraulically or pneumatically.
If the fly ash handling system is not designed as per the required application, it could lead to various challenges. Some of which include the following.
1. No-flow from Hopper or Silo Outlet
In fly ash handling, the no-flow condition can be caused either due to rat-holing or arching.
- In rat-holing, the material forms a hole or narrow channel above an outlet. This is caused due to the material’s cohesive strength, which hinders the flow of the material into the channel, leading to a no-flow condition.
- In arching (bridging), the material being discharged forms a bridge or arch over the outlet, resulting in a no-flow condition.
Both of these conditions can be resolved by identifying the issue, which could be the hopper design, vibration, conditioning screws or fluidizing nozzles. Once the problem with the product flow is identified, you can work on finding a solution for it.
For instance, depending on the characteristic of the material, if the issue is the hopper design, you can use conical and angled hoppers. These can help create a seamless flow path for the material, preventing bridging and rat-holing issues.
2. Flow Rate Limitation
Due to its fine particle size distribution, the permeability of fly ash is very low, which makes it considerable resistance to airflow and other gases.
During the discharge from a hopper outlet or a silo, the air counter-flows through the fly ash bed, providing an opposing gravitational force, which obstructs the discharge process. This obstruction (limitation) increases the unloading time and the time required to fill the trucks. Slow unloading from the storage silo can also lead to storage issues for newly collected fly ash.
3. Flooding or Uncontrolled Flow
Another fly ash challenge is that the fine particle sizes (fine powder) can turn to fluid due to the presence of air, which can cause flooding. Unless the feeder contains it, fly ash can become fluidised and flush through the outlet. This can lead to uncontrolled flow, making it difficult to meter the discharge. Plus, it can harm the environment and increase health risks.
4. Structural Problems
In the event, the rat-holes or the arches collapse, the force of it could lead to catastrophic structural damage. Erratic flow channels within the silo can also result in non-uniform loading along the outer walls. This, in turn, can cause the silo to wrinkle or buckle or lead to cracks and dents, which could be potentially dangerous for all.
5. Wear and Dust Generation
Fly ash is very abrasive and frictional due to the presence of excessive silicon dioxide. When conveying it, the material handling system can undergo tremendous wear and tear. This can lead to costly repairs and frequent replacement.
Likewise, the dust generated when conveying fly ash is highly toxic, which raises safety concerns. Dusting can occur at transfer points or when the air currents pick up particles from the pile. Thus, proper measures need to be undertaken to control dust emissions.
Other Problems
- Sometimes, fly ash can contain excess unburned carbon, which, if stored in an aerated bin, can lead to combustion that can be hazardous.
- Fly ash can cause plugging in pneumatic conveying lines and lead to pipeline wear issues.
- Handling fly ash with air slides or aerated bin bottoms can cause flow problems, leading to incomplete discharge or flow rate limitations.
Learn How Fly Ash Is Transforming the Cement Industry
B] Where is Fly Ash Used?
1. Portland Cement Concrete (PCC)
Fly ash is an excellent replacement for Portland cement in concrete.
- The use of fly ash as a substitute for Portland cement is particularly suitable as it is resistant to freezing damage.
- Fly ash can also be used in higher dosages in some applications.
- In addition, fly ash can make the concrete more durable and increase its resistance to chemicals.
Supporters of fly ash assert that replacing Portland cement with fly ash reduces the greenhouse gas “footprint” of concrete. For instance, it has been noted that the production of a single ton of Portland cement generates roughly one ton of CO2. Whereas, fly ash doesn’t generate any CO2.
2. Soil and Road Base Stabilisation
Soil stabilisation means a permanent chemical and physical alteration of soils to improve their physical properties. Stabilisation increases the sheer strength of the soil, thereby improving its load-bearing capability.
A blend of fly ash and lime products can be used for different geotechnical applications, which are common in highway construction. This blend of materials can help strengthen & stabilise embankments, control shrink-swell properties of expansive soils, and reduce soil moisture content, allowing for compaction.
3. Flowable Fills
Instead of compacted earth or granular fill, fly ash can be used to produce flowable fill, which is used for self-levelling and self-compaction. Usually, to produce flowable fill, mixtures of Portland cement and filler materials are used along with mineral admixtures. Here, as a filler material, fly ash can be used instead of Portland cement or fine aggregate (river sand).
4.Waste Treatment and Stabilisation
Since fly ash has water absorption capabilities, it can be used in combination with other alkaline materials to convert sewage sludge into biofuel or organic fertiliser.
5.Catalyst
When treated with sodium hydroxide, fly ash appears to function as a catalyst for converting polyethene into a substance similar to crude oil in a high-temperature process. This process is called pyrolysis and is used for wastewater treatment. In addition, fly ash may be used in the stabilisation process of contaminated soil or hazardous waste.
Learn How Fly Ash Is Transforming the Cement Industry
Fly Ash Handling Solutions: Macawber Ash Handling Conveying Systems
As a leading manufacturer of pneumatic conveying systems, we offer comprehensive solutions for all – bottom ash, bed ash, and fly ash handling. Our ash handling equipment is designed by considering various factors – distance, density, conveying capabilities and safety. Depending on your needs, we offer ash handling systems in different transfer modes – dense phase and dilute phase. We also ensure that our ash handling system complies with stringent industry standards.
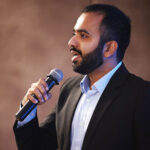
Kedar Kamath
Kedar Kamath is a highly accomplished bulk material handling professional with 14+ years of experience at Macawber Engineering Systems India Pvt Ltd. Starting as a junior sales engineer, he progressed to his current role heading Business Development and Sales. His expertise encompasses proposals, estimations, sales, marketing, design engineering, project execution, and factory operations. Mentored by industry leaders, Kedar's technical acumen (B.Tech in Electrical Engineering, VJTI, Mumbai) and innovative approach deliver tailored solutions. He's passionate about sustainable practices and driving excellence within the industry.