In the steelmaking industry, blast furnaces are at the heart of iron production. These massive, continuous reactors rely on the precise and consistent delivery of raw materials to function efficiently. These materials include fine powders, such as pulverised coal, hydrated lime, dolomite, various industrial dusts, and occasionally, fluxes or additives. Transporting these materials effectively, without causing degradation or excessive dust emissions, is critical. This is where dense phase pneumatic conveying becomes an essential part of the process.
Now, let’s understand the basics of a dense phase conveying system for blast furnaces, its characteristics, application, and design features comprehensively.
What Is Dense Phase Conveying?
Dense phase conveying is a method of pneumatic transport in which bulk solids are pushed through pipelines at low velocities using compressed air or inert gas. Unlike dilute phase systems, which operate at higher speeds and carry materials suspended in airflow, dense phase systems convey material in a more controlled, plug-flow or slug-flow pattern.
Key Characteristics:
- Low conveying velocity (typically < 4 m/s)
- High material-to-air ratio
- Gentle handling of materials
- Lower wear and tear on equipment
These features make dense phase conveying especially suitable for abrasive, fragile, or segregative materials related to blast furnace conveying systems and operations.
Boost conveying efficiency in your blast furnace.
Applications in Blast Furnace Operations
1. Cast House Dust
In a blast furnace cast house, dense phase pneumatic conveying systems are used to efficiently handle valuable dust from the bag filter. Due to its low-velocity and high-pressure operation, dense phase conveying minimises wear on pipelines and prevents material degradation. It ensures dust-free and enclosed transport, critical in the harsh and high-temperature cast house environment. Macawber has successfully transferred baghouse dust to recycling silos. The system’s reliability and minimal maintenance make it ideal for continuous-duty cast house operations, enhancing both safety and environmental compliance in modern steel plants.
2. Stock House Dust
In a stock house, dense phase pneumatic conveying is used for the efficient and dust-free transport of fine raw materials, such as iron ore fines, sinter coke, fluxes, and coal dust, to storage bins or charging hoppers. Dense phase conveying ensures enclosed handling, critical for maintaining a clean environment and preventing material loss during transfer. Its reliability and precision make it ideal for feeding batching systems and maintaining consistent burden quality, which is essential for stable blast furnace operation and optimal process control.
3. Pulverised Coal Injection
In blast furnace operations, pulverised coal injection (PCI) uses a dense phase pneumatic conveying system to transport finely ground coal from storage to the tuyere zone. The system includes coal silos, pressure vessels, pipelines, and flow control valves. It delivers coal directly into the blast furnace through lances, reducing coke consumption and enhancing combustion efficiency. Dense phase systems ensure accurate, reliable, and dust-free coal delivery, critical for maintaining stable furnace operation and reducing fuel costs. Macawber is well equipped with pneumatic conveying and a high-pressure injection system for such a specific application.
4. Gas Cleaning Plant
The blast furnace generates gases that are directed to a gas cleaning plant. In a gas cleaning plant, a gravity dust catcher or cyclone separator is installed for dry scrubbing of these high-temperature, high-pressure gases coming from the blast furnace. The Macawber’s inflatable seal type pressure-rated dome valve, a specialised valve designed for high-pressure applications, particularly in pneumatic conveying systems, has successfully cemented its place in handling this type of dust application. Due to the effectiveness of our system, we have supplied thousands of pneumatic conveying systems for blast furnace dust transfer.
Critical Design Features
Keeping heavy dust in the blast furnace in mind, Macawber offers the following design customisation:
1. Durable Components
Macawber supplies bends with heavy-duty liners made from materials such as cast basalt, alumina-based ceramic, and DRC (Densified Reinforced Composite). Cast basalt bends feature miter-type joints with liners baked in a furnace, while alumina-based ceramic bends utilise tiles of alumina-based ceramic. DRC bends incorporate a cold-rolled cement-based composite. These liners can be designed with similar hardness and thickness, ranging from 10 mm to 25 mm.
2. Heavy-duty Designs
Incorporation of special liners and coatings in the internals of our conveying pressure vessels (Denseveyor), dome valves, and diverter valves makes our systems durable and heavy-duty.
Products Handling Heavy Dust in Blast Furnace Application
Macawber offers a range of products that provide effective blast furnace material handling capability while handling heavy powders, including:
- Denseveyor
- Controlveyor
- Dome valves
- Diverter valves
- Bag filters
- Wear-resistant bends
- Bin vent filters
- Boosting arrangement
Boost conveying efficiency in your blast furnace.
Conclusion
Dense phase conveying systems are crucial for transporting the required materials to the blast furnace. It ensures minimal material degradation and wear of materials being transported. Macawber Engineering is the top manufacturer and supplier of pneumatic conveying systems in India. With our innovative, reliable blast furnace conveying solutions and commitment to quality, we have positioned ourselves as a leader in the heavy dust handling, addressing the unique challenges associated with the blast furnace. Contact us today.
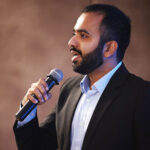
Kedar Kamath
Kedar Kamath is a highly accomplished bulk material handling professional with 14+ years of experience at Macawber Engineering Systems India Pvt Ltd. Starting as a junior sales engineer, he progressed to his current role heading Business Development and Sales. His expertise encompasses proposals, estimations, sales, marketing, design engineering, project execution, and factory operations. Mentored by industry leaders, Kedar's technical acumen (B.Tech in Electrical Engineering, VJTI, Mumbai) and innovative approach deliver tailored solutions. He's passionate about sustainable practices and driving excellence within the industry.