Material handling is a pivotal part of the supply chain process. They are needed to optimise the movement of goods and materials in manufacturing and storage facilities. A well-structured material handling system can improve customer service, reduce costs, and eliminate the risk of accidents.
Diverter valves play a crucial role in material handling systems, redirecting material flow in pipelines and ensuring efficient routing. This blog aims to guide readers in selecting the optimal diverter valve for their specific material handling requirements.
A] What Are Diverter Valves And What Are They Used For?
A diverter valve is a specialised, automated valve that directs the flow of Powder, pellets, granules, flakes etc. from one source to another. These valves are designed to handle operating pressures, corrosive environments, and high temperatures.
Diverter valves are a key component in different industries as they ensure the efficient and safe transfer of Powder without any contamination. They are essential in the food processing industry for sorting grains, powders, and ingredients, as well as pharmaceuticals for diverting medications and ingredients.
The valve is also used in mining-based industries for crushed powders of minerals and in the agricultural sector to sort grains and seeds. They are also crucial in manufacturing processes such as plastics, chemicals, and building materials, where precise material handling and routing are vital for maintaining efficiency and product quality throughout production and distribution processes.
Consult a reputed pneumatic conveying systems manufacturer to invest in the right one for your specific industrial application.
Understand more about the Diverter valves here!
B] Types of Diverter Valves
Diverter valves are available in various types. Each type is designed to suit specific material handling needs. Choosing a diverter valve that meets your application requirements is extremely crucial. Let’s discuss about different types of diverter valves;
- DV Type Diverter Valve: These valves and diverters typically featured with Macawber Dome valve to divert material flow from one inlet to two outlet or one inlet to multiple outlets & vice-versa, ensuring efficient distribution.
- Switch Valve: These are T-type inline material diverters With one inlet to two outlet or one inlet to multiple outlets & vice-versa configuration. Actuation can be pneumatic hydraulic or motorized.
- Dump Valve: Dump valves allow material to be discharged quickly and efficiently into designated containers or downstream processes. It is primarily used for gravity-fed applications. Used to divert material from one silo to another (incase of in-line silos).
- Tunnel-Type Diverter Valve: These valves provide a smooth transition for materials flowing through pipes or chutes, redirecting them without causing excessive turbulence or pressure drops.
- Multioutlet Diverter Valve: Designed to handle multiple discharge points simultaneously, these valves enable precise distribution of materials into different processing or packaging lines, enhancing operational flexibility.
C] Factors To Consider When Choosing a Diverter Valve
Choosing the right diverter valve involves considering several essential factors to ensure it meets the specific requirements of your material handling process. Make sure to conduct a thorough assessment of different factors to ensure compatibility with your material handling system requirements.
This will boost operational efficiency and meet long-term reliability expectations. You can also consult with experienced engineers or valve specialists who can provide valuable insights and recommendations tailored to your specific application needs.
Here, let’s check out the key factors to consider when choosing a diverter valve:
1. Material Compatibility
The foremost consideration is the compatibility of the diverter valve with the material handling system. There are different material types with varying characteristics, such as abrasiveness, particle size, and flow properties. It can affect valve performance and longevity. For example, abrasive materials like sand require valves with durable materials and wear-resistant components to withstand erosion over time. Food-grade materials also necessitate valves constructed from stainless steel to ensure compliance with hygiene standards.
2. Flow Rate and Capacity
Understanding the flow rate and capacity requirements is necessary for selecting a diverter valve that can handle the anticipated material volume. The important factors to assess include flow rates. It will let you determine the maximum and minimum flow rates the valve needs to handle under normal operating conditions. The next factor is to consider the total material volume that the valve will process within a given time frame. You need to choose a diverter valve with a capacity that matches your system’s requirements and prevents bottlenecks. Moreover, it ensures smooth material flow without compromising efficiency.
3. System Pressure and Temperature
Valve performance is significantly influenced by the operating conditions of your system, including pressure and temperature. When considering pressure rating, select a diverter valve for pneumatic conveying that can withstand the maximum system pressure without structural failure or leakage. This is particularly critical in pneumatic conveying systems where pressures can significantly vary. The next consideration is the temperature range. This ensures the valve materials and seals are compatible with the operating temperatures. High temperatures can affect valve performance and longevity when not properly accounted for.
4. Seal Type and Leakage Prevention
Effective sealing is highly necessary to prevent leakage and maintain system efficiency. You need to choose seal materials that are compatible with your material and environmental conditions like temperature and chemical exposure. Check out the sealing mechanism that can evaluate the type, such as inflatable seals, based on the operational requirements and application pressure. Know about its leakage prevention capability to ensure the valve design and sealing arrangement minimise the material leakage risk, as this can affect product quality, safety, and environmental compliance.
5. Ease of Maintenance and Installation
The ease of maintenance and installation can impact downtime and operational efficiency. Go for valves that allow easy accessibility to internal components for inspection, cleaning, and maintenance. Check out maintenance requirements that consider factors such as lubrication needs, recommended service intervals, and wear parts replacement. You need to understand installation flexibility and choose valves that are compatible with your existing piping layout and space requirements to simplify integration into your system.
6. Quality And Reliability
When selecting a high-quality diverter valve from a reputable manufacturer, ensure reliability and longevity. Research about the manufacturer’s reputation. Check their track record, certifications, and customer reviews to evaluate product quality and reliability. Go through its material and construction to evaluate the materials used in valve construction, such as stainless steel, cast iron. This will ensure durability and resistance to corrosion or wear. Do not forget to check their testing process and certification. You need to look for diverter valves that meet industry standards and certifications relevant to your application.
Understand more about the Diverter valves here!
Conclusion
This is your comprehensive guide to choosing the right diverter valve. When choosing a diverter valve, it is necessary to consider material compatibility, flow rates, system pressures, sealing effectiveness, ease of maintenance, and overall quality. Each of the factors impacts the performance, longevity, and reliability of the valve within your material handling system.
Making an informed decision on selecting the right diverter valve ensures seamless operation, minimises downtime, and optimises efficiency. By prioritising essential considerations, you can confidently choose a diverter valve that not only meets immediate operational needs but also aligns with long-term performance expectations, enhancing overall productivity and ensuring a reliable material handling process. If you are ready to make a purchase, contact us.
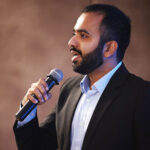
Kedar Kamath
Kedar Kamath is a highly accomplished bulk material handling professional with 14+ years of experience at Macawber Engineering Systems India Pvt Ltd. Starting as a junior sales engineer, he progressed to his current role heading Business Development and Sales. His expertise encompasses proposals, estimations, sales, marketing, design engineering, project execution, and factory operations. Mentored by industry leaders, Kedar's technical acumen (B.Tech in Electrical Engineering, VJTI, Mumbai) and innovative approach deliver tailored solutions. He's passionate about sustainable practices and driving excellence within the industry.